In the ever-evolving landscape of the manufacturing industry, maintaining impeccable quality control is paramount. The advent of visual inspection systems has brought about a transformative shift, enhancing precision, efficiency, and reliability in quality assurance processes. This article delves into the multifaceted ways in which visual inspection systems are revolutionizing quality control in the manufacturing industry.
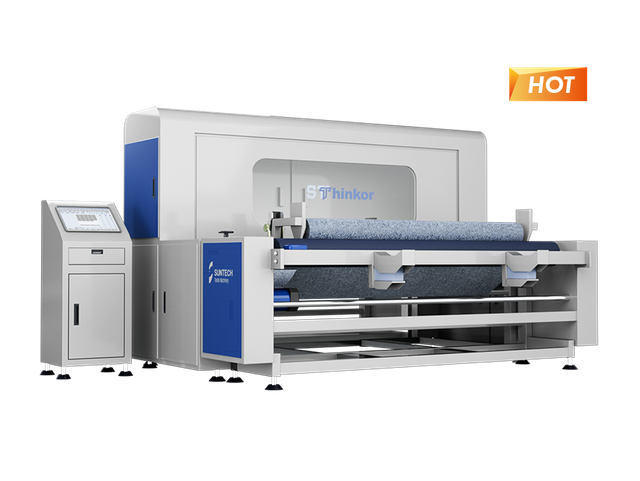
Enhanced Accuracy and Precision
One of the most significant advantages of visual inspection systems is their unparalleled accuracy and precision. Traditional manual inspections are prone to human error, fatigue, and inconsistency. In contrast, automated visual inspection systems utilize advanced imaging technologies and algorithms to detect even the minutest defects with remarkable consistency. For instance, in the electronics manufacturing sector, these systems can identify microscopic soldering flaws that might go unnoticed by the human eye, ensuring that only flawless products reach the market.
Increased Efficiency and Speed
Efficiency is a critical factor in the competitive manufacturing industry. Visual inspection systems significantly expedite the quality control process by automating the inspection of products at various stages of production. This not only reduces the time required for inspections but also minimizes production bottlenecks. For example, in the automotive industry, visual inspection systems can rapidly scan and analyze components on the assembly line, allowing for real-time quality assessments and immediate corrective actions, thereby streamlining the entire production process.
Cost-Effectiveness and ROI
Implementing visual inspection systems can lead to substantial cost savings in the long run. While the initial investment in these systems might be significant, the reduction in labor costs, minimized rework, and decreased product recalls contribute to a favorable return on investment (ROI). In the pharmaceutical industry, for example, visual inspection systems can ensure that packaging and labeling are flawless, reducing the risk of costly recalls due to labeling errors. This not only saves money but also protects the brand's reputation.
Data-Driven Insights and Continuous Improvement
Another revolutionary aspect of visual inspection systems is their ability to generate valuable data and insights. These systems can collect and analyze vast amounts of data related to product quality, defect patterns, and production trends. Manufacturers can leverage this data to identify root causes of defects, optimize production processes, and implement continuous improvement strategies. In the food and beverage industry, for instance, visual inspection systems can monitor packaging integrity and provide data on common defects, enabling manufacturers to enhance their packaging processes and reduce waste.
Adaptability and Scalability
Visual inspection systems are highly adaptable and scalable, making them suitable for a wide range of manufacturing environments. Whether it's a small-scale operation or a large industrial facility, these systems can be customized to meet specific inspection requirements. In the textile industry, for example, visual inspection systems can be tailored to detect defects in fabrics, such as tears, stains, or color inconsistencies, ensuring that only high-quality textiles are delivered to customers.
In conclusion, the integration of visual inspection systems in the manufacturing industry is a game-changer, revolutionizing quality control processes. By enhancing accuracy, increasing efficiency, providing cost-effectiveness, offering data-driven insights, and ensuring adaptability, these systems are setting new standards for quality assurance. As technology continues to advance, the role of visual inspection systems in the manufacturing industry will only become more pivotal, driving innovation and excellence in quality control.