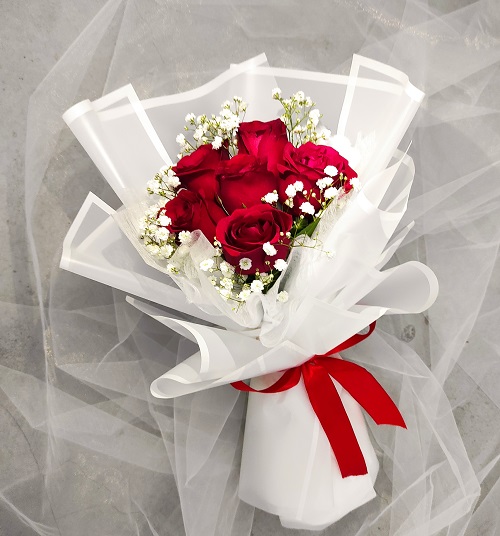
About Us
Your go-to destination for exquisite flowers and heartfelt floral arrangements. We are passionate about creating stunning bouquets that add beauty, love, and joy to every occasion.
Our Services
Anniversary Flowers
Anniversaries are special, and nothing expresses love better than a thoughtfully arranged anniversary bouquet. From classic red roses symbolizing passion to elegant lilies and orchids for a sophisticated touch, we design floral arrangements that make every anniversary memorable.
Same-Day Flower Delivery
Life is full of surprises, and sometimes, last-minute flower deliveries are necessary. With our same-day flower delivery service, you can send fresh flowers anywhere
Custom Floral Arrangements
At Mind Meow, we believe that flowers should be as unique as the person receiving them. That’s why we offer custom floral arrangements tailored to your preferences.
Corporate & Event Floral Services
Flowers enhance any space, adding elegance, freshness, and warmth. We provide customized floral services for businesses, offices, and events to create a lasting impression.
Sympathy & Condolence Flowers
During times of loss, flowers serve as a comforting gesture, offering support and heartfelt condolences. Our sympathy flower arrangements are thoughtfully designed to bring peace and solace to grieving families.
Birthday & Celebration Bouquets
Nothing says “Happy Birthday” better than a fresh, vibrant bouquet! Our birthday flower arrangements are designed to bring happiness and joy to your loved ones.
Latest News
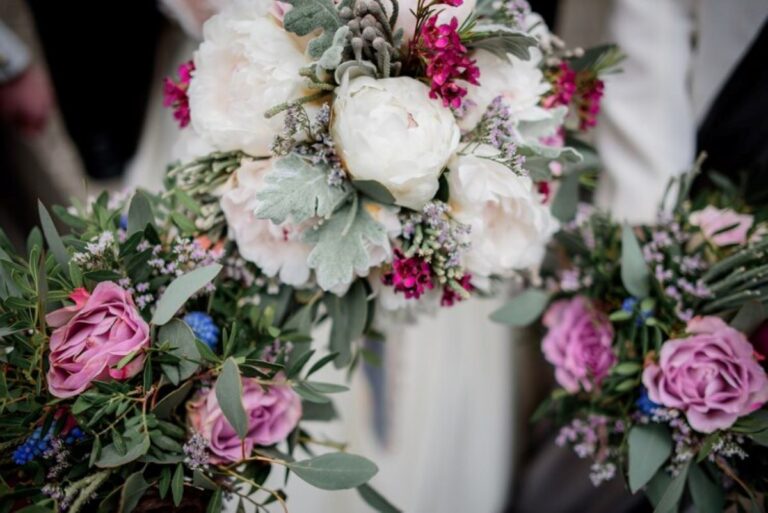
Find the Best St Leonards Flower Delivery for Every Occasion
When it comes to expressing emotions, flowers have an unparalleled ability to convey sentiments…
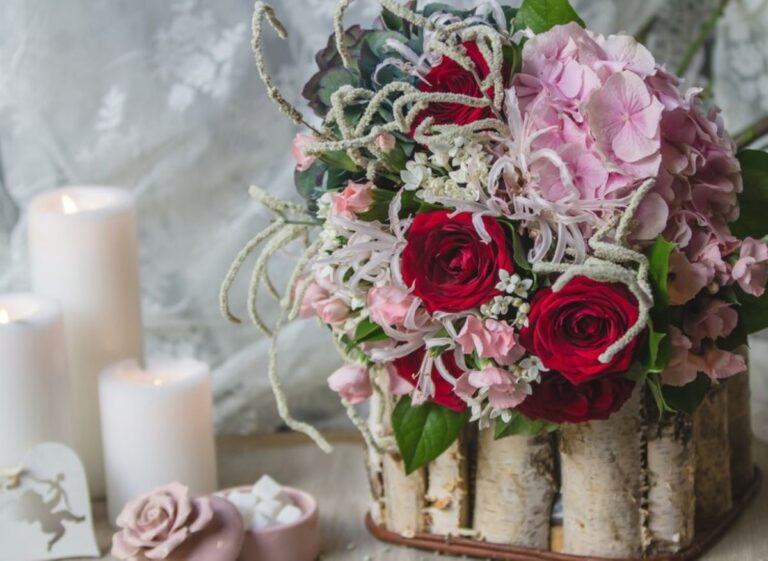
St Leonards Florist: Top Picks for Fresh and Beautiful Flowers
In the vibrant suburb of St Leonards, the floral scene is as diverse as…
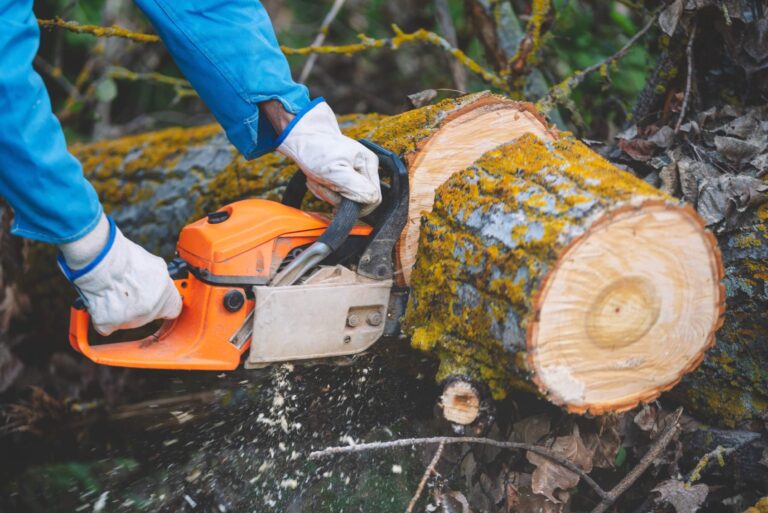
Tree Removal Hills District: Reliable Services for Your Home
Understanding the Importance of Tree Removal Tree removal is a crucial aspect of maintaining…
Why Choose Us?
We believe that flowers are more than just gifts—they are expressions of love, celebration, and heartfelt emotions. As a trusted florist serving Mosman flowers, Neutral Bay, North Sydney, Cammeray, Northbridge, and Milsons Point, we take pride in delivering fresh, high-quality floral arrangements with exceptional service.
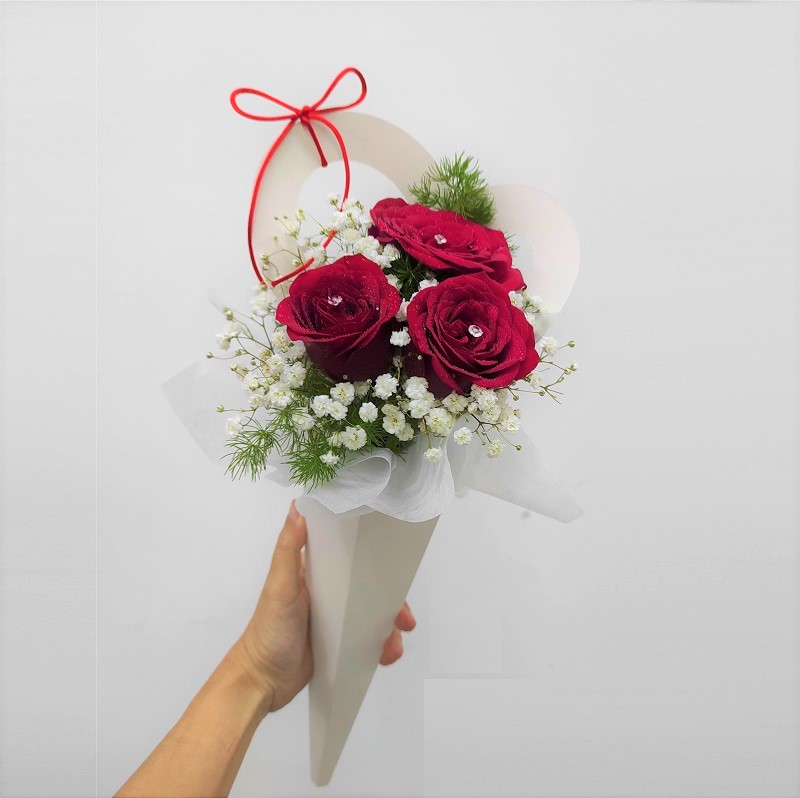
What Our Customers Say
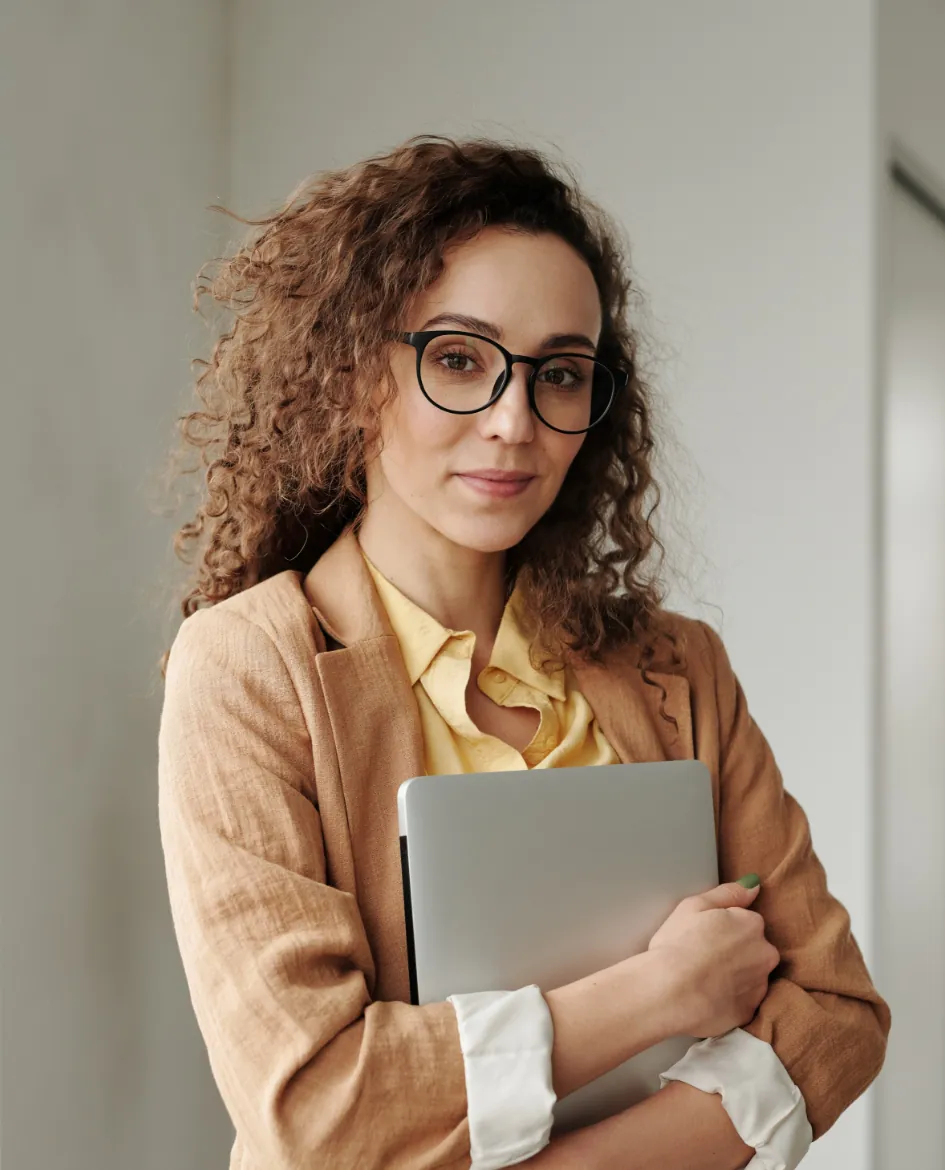